Zapotec master weaver José Buenaventura González Gutierréz shifts his weight from one long wooden pedal to the other. Both pedals are attached to a tree stump near the wall. As Gutierréz switches pedals, he throws in the wooden bobbin holder of dyed fabric in-between layers of cotton strings and catches it with his other hand. He lifts the wool up, making it taut between the cotton strings and presses it down with another part of the loom. This is the beginning of the weaving process. It’s the last transition of the fabric into the rug that Gutierréz will make.
On Sunday Dec. 5, there was a demonstration hosted by LocalFiber’s seasonal pop-up shop. For a little over two hours, people came and spectated as Gutierréz weaved together the start of the rug.
About the Demonstration and the Weaver
Gutierréz said that part of the reason why he gives demonstrations is so that people will see the work behind the rugs, so that will also help them to understand the price and also so that people can see their own potential in creating.
“I want people to know how to weave. . . , all of us can do something. . .it makes us more productive,” Gutierréz said.
As viewers gathered around the loom and watched, they asked questions as encouraged by Gutierréz whenever someone new came to watch. He even provided a space for those watching to try to weave a few lines of fabric on the loom.
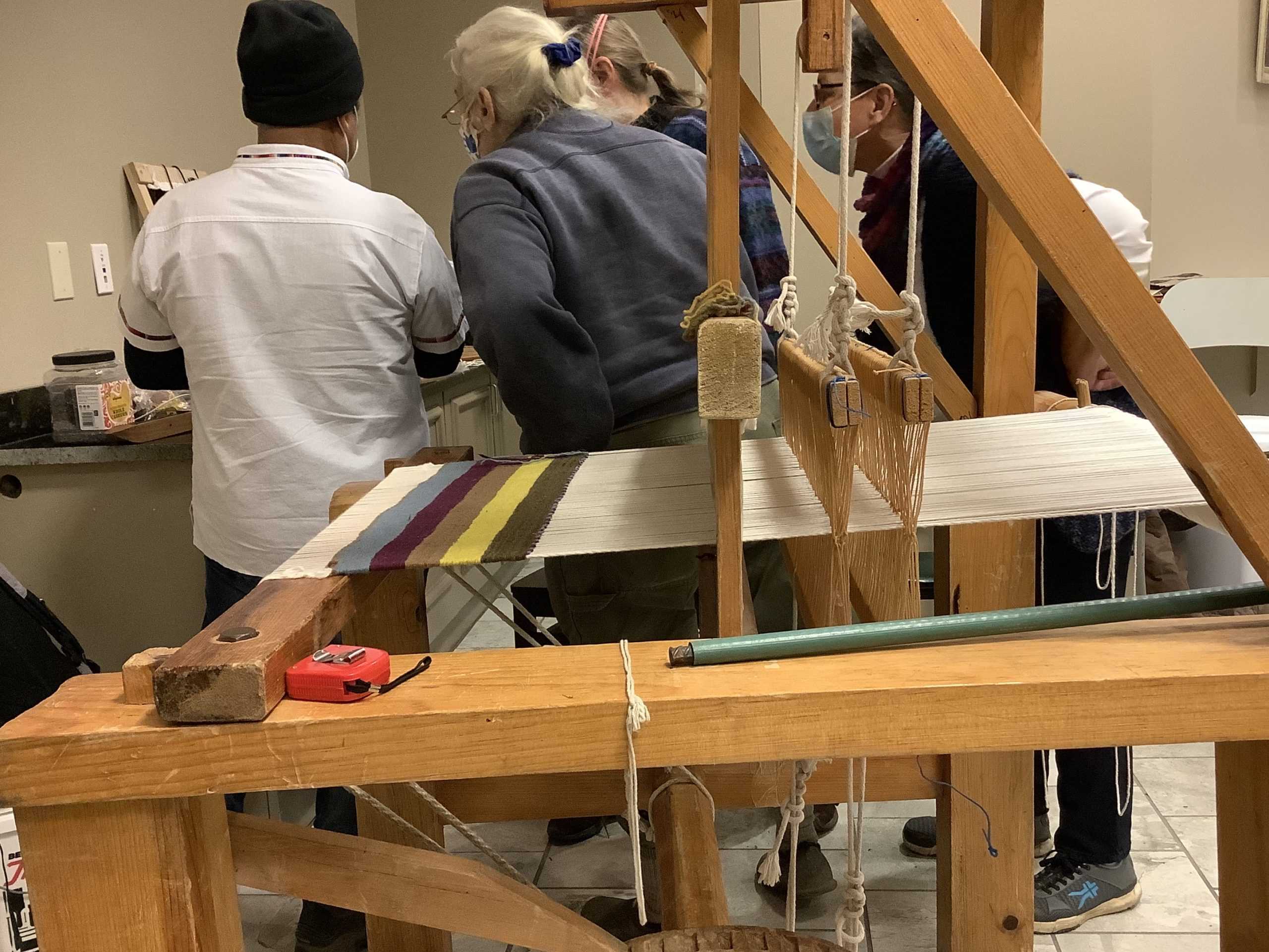
Gutierréz gave an opportunity for learning about weaving, a craft in which he’s been doing for over 50 years. At a young age, he learned to weave from his father.
“I started when I was ten years old—a long time ago, let’s call it that,” Gutierréz said.
From Teotitlan del Valle in Oaxaca, Mexico, Gutierréz stems from a generation of weavers.
“My father was a weaver, my grandfather and my great-grandfather definitely,” he said.
The Loom
Gutierréz said that the loom he worked on, is a portable loom that he brings to shows like this one, and that setting up the loom properly is important for efficiency and less problems when weaving.
“If you set everything up well, you can keep going,” Gutierréz said.
There are many different components to the loom including the warp, which is the cotton strings that he wrapped from back to front to back again on the beams of the loom. Also, the pedals of the loom are tied to and control the harness. The harnesses are the frames that hold the warp threads.
“Each pedal is one of the harnesses, the pedals control the harnesses,” Gutierréz explained .
A few times Gutierréz adjusted sections of the loom to realign the height and to make sure everything was even. Because of the smoother flooring being a bit slippery, the stump and pedals were sliding. Gutierréz told me that he sometimes has two beams he sets up for the loom that help it remain sturdy.
“Like you know your car, you need to know your loom,” Gutierréz said.
The Fiber
The kind of wool that Gutierréz uses in Mexico is called churro, but what he’s using now is mostly mohair or alpaca. For the wool to be used for weaving, the material has to go through a series of procedures beforehand. Once the wool is sheared from the sheep, the wool gets carded, washed, cut, spun, dyed and then it’s ready for weaving.
For the dying process, Gutierréz does this himself through natural dyes. To create red, he uses cochineal, which is a bug that lives on cactus from his home town in Oaxaca. The blues are created from indigo, which is longer (it takes weeks) but is an enjoyable process.
“I love it, it’s very beautiful, you have to be exact with it,” Gutierréz said.
About the Pop Up Shop
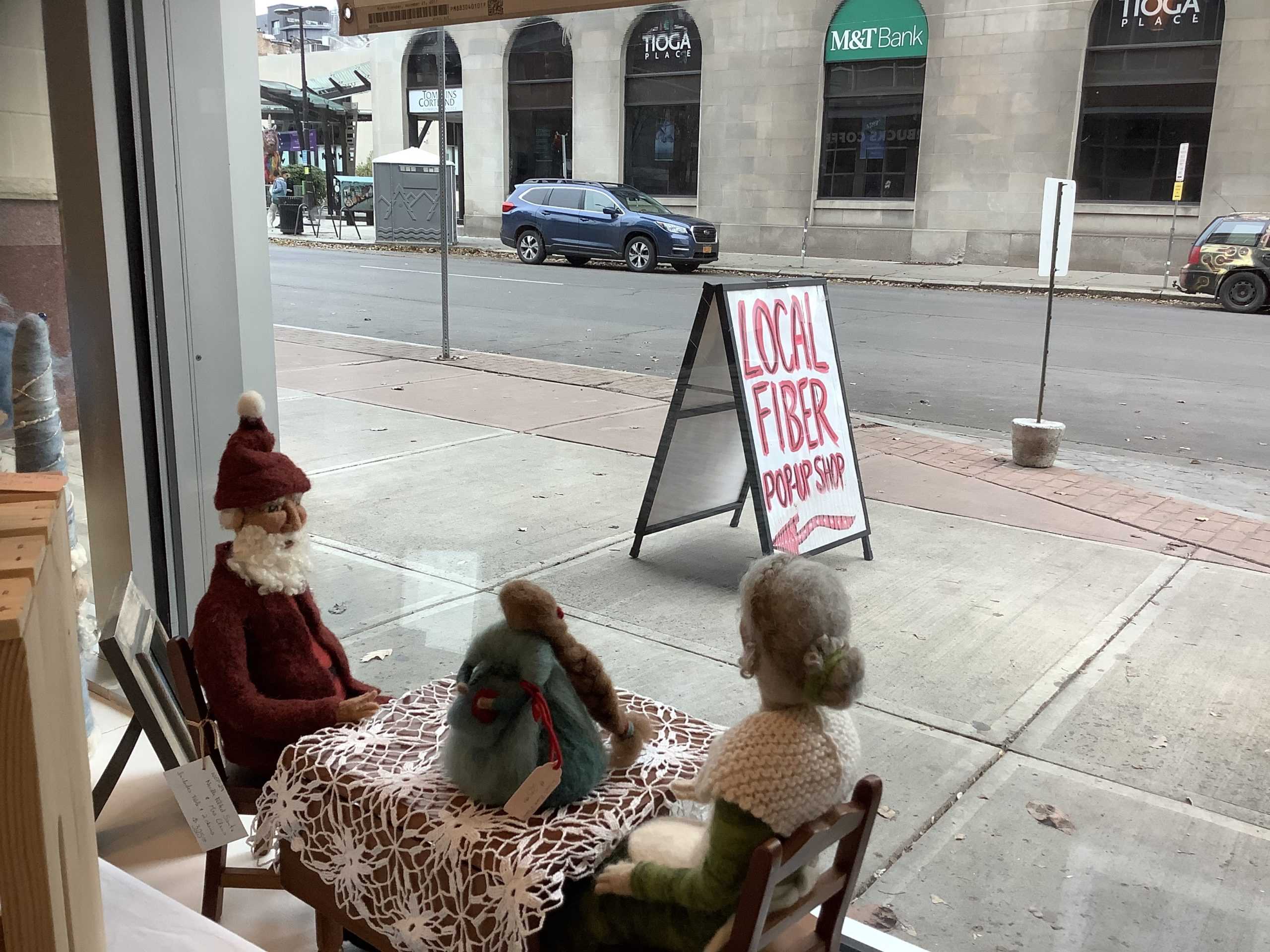
The LocalFiber Pop Up shop is open until the end of December. The shop sells many different fibers and in different stages from locks straight from the sheep that are unspun to already crafted hats, gloves and scarfs. Noreen Atkins, the treasure for Local Fiber showed the shop and the different kinds of fibers, describing their qualities, their uses and their origins.
Atkins described that hats, gloves, rugs, blankets and even suits could be made from wool. She also said that mohair is from goats, and angora wool is from rabbits.
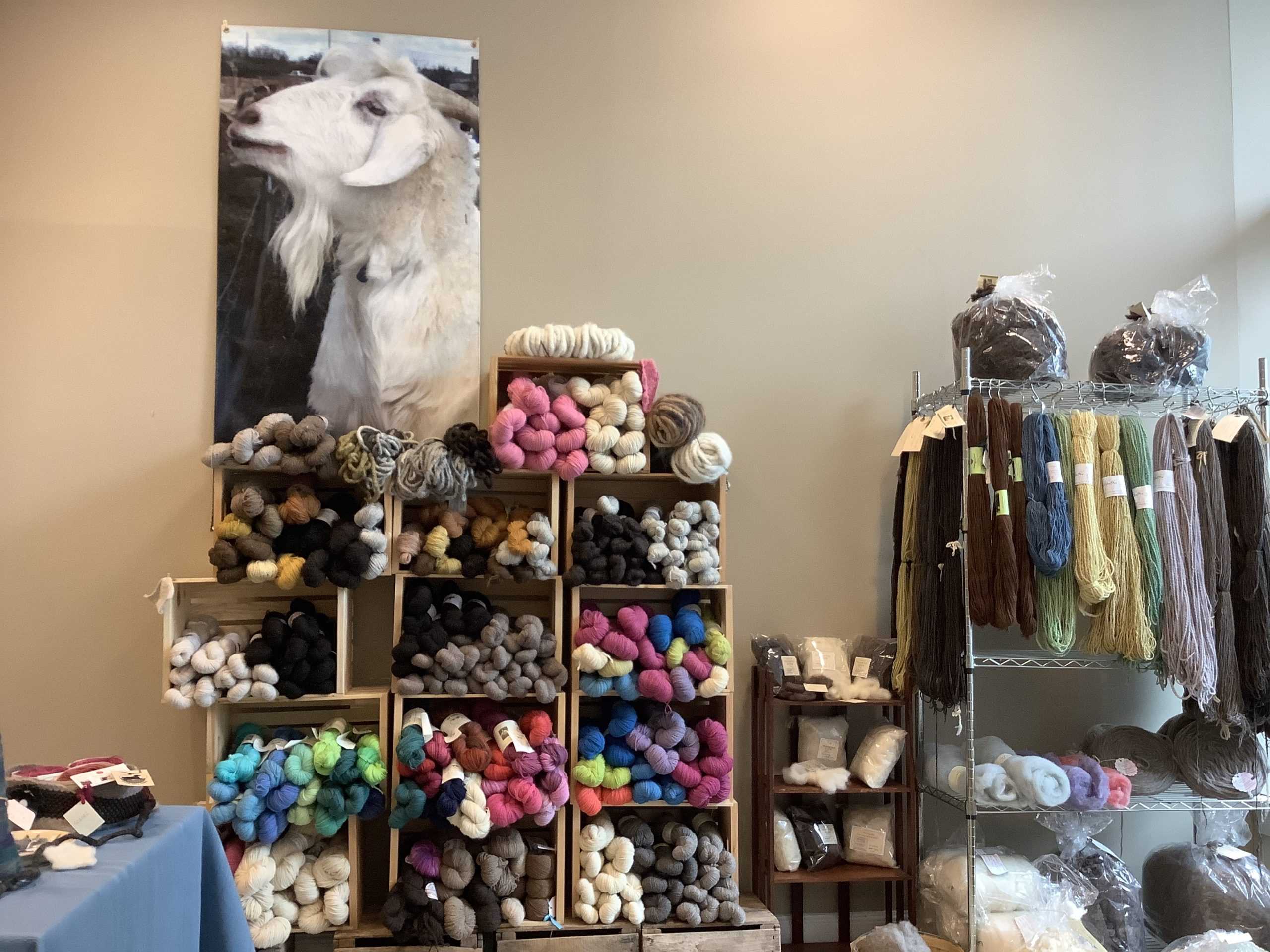
When asked about the members role for the LocalFiber popup shop, Atkins responded by saying “We’re farmers taking turns managing the shop. There are a lot of executive board members around.”
Another member of the board for LocalFiber President Amy Glaser spoke on the reasons behind the pop up shop and the organization.
“We do this as a way to promote our own farms and the availability, diversity and the use of sustainable fibers. . . . For all of us, we love to share our passion for fiber and what you can use it for. It predates written history, so it connects us to the past and hopefully the future. It’s not limited to just farmers but also is open to fiber artists like Jose and fiber users,” Glaser said.